Lieknos gamybos koncepcija Rusijos įmonėse buvo įdiegta ne taip seniai, palyginti su užsienio šalimis, kur Kaizeno filosofija pradėta taikyti praėjusio amžiaus 5 dešimtmetyje. Prieš dešimtmetį tik trečdalis Rusijos pramonės įmonių buvo suinteresuotos optimizuoti gamybą. Dabar efektyvių gamybos sistemų statybą, be diskretiškos pramoninės gamybos ir konsultavimo, naudoja ne tik stambios, bet ir vidutinės įmonės daugelyje ekonomikos sektorių.
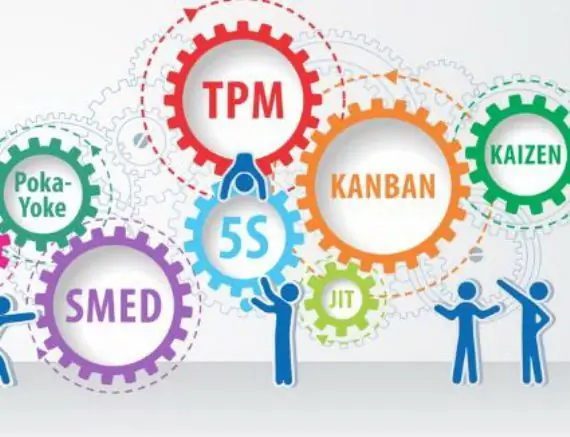
Liesos gamybos sistemos pradininkai yra automobilių gigantai „Ford“ir „Toyota“. Tarp užsienio kompanijų, sėkmingai taikančių „Lean“gamybos principus, tokių kaip „Nike“, „Textron“, „Parker“, „Intel“. Aktyvaus „Lean“technologijų naudojimo mūsų šalyje pradžia laikoma 2006 m., Kai įvyko pirmasis Rusijos „Lean“forumas. Kuriant vidaus liesos gamybos sistemas, pionieriai yra garsūs mūsų automobilių gamintojai - GAZ ir KAMAZ. Tarp įmonių, naudojančių „Lean“optimizavimo sistemas ir metodus, pirmauja „Rusal“, „Rosatom“, „Eurochem“, TVEL, „Sberbank“ir daugelis kitų.
Lengvos gamybos logistikos įgyvendinimas Rusijos įmonėse turi valstybės paramą ir ją reguliuoja pagrindiniai standartai: GOST numeriai R 57522-2017, R 57523-2017, R 57524-2017, taip pat pramonės rekomendacijos, patvirtintos Pramonės ministerijos įsakymu. ir prekyba.
Terminas „Lean manufacturing“arba LIN yra semantinis vertimas į angliškus apibrėžimus „lean manufacturing“, „lean production“ir jų santrumpos LEAN transkripciją.
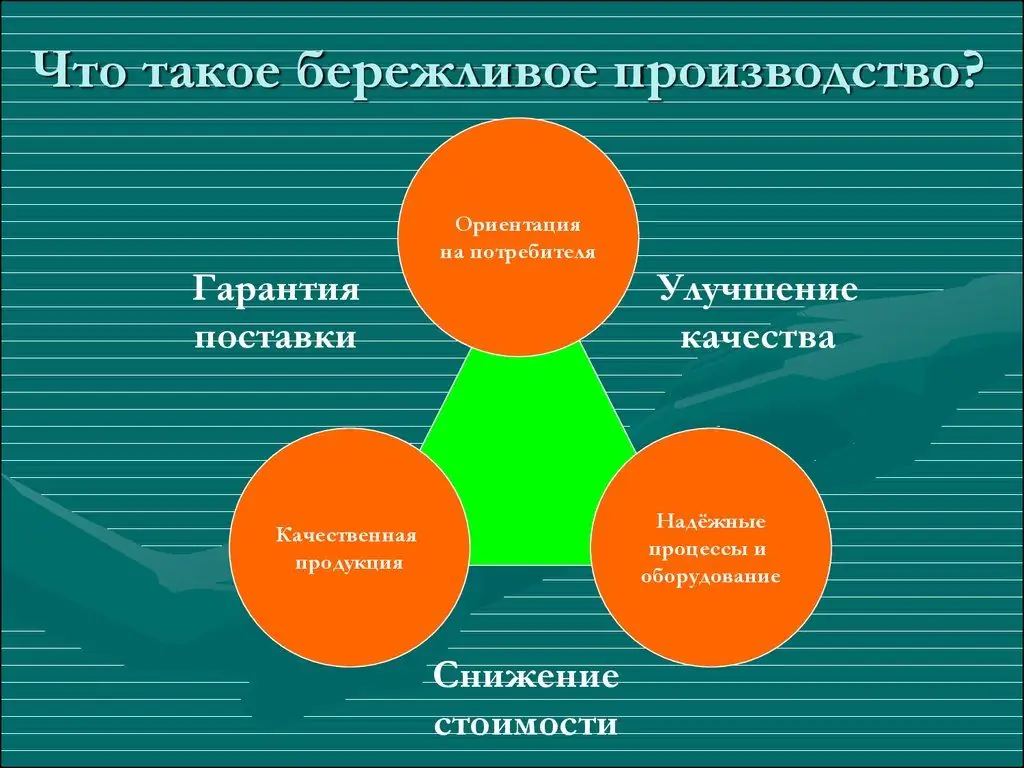
„Lean“gamyba suprantama kaip įmonės valdymo sistema, leidžianti pagerinti darbo kokybę, kartu sumažinant išlaidas, sumažinant nuostolius.
Anglų ir rusų kalbos žodis liesas yra „liesas, liesas, lieknas“. Norėdami tapti tokiais, turite prarasti riebalų perteklių. Kalbant apie gamybos sritį, tai reiškia, kad būtina atsikratyti nuostolių ir taip sumažinti išlaidas. Todėl liesa gamyba kartais vadinama liesa.
Trys LIN gamybos koncepcijos
„Lean“gamybos esmę apibūdino G. Fordas, sakydamas:
„Lean“gamybos sistemoje du aspektai yra esminiai:
- Į optimizavimo procedūras būtina įtraukti kiekvieną įmonės darbuotoją.
- Įmonė turėtų būti maksimaliai orientuota į vartotojo interesus.
Konceptualiai pasaulinė gamybos optimizavimo sistema yra pagrįsta trimis principais.
- Kaizeno filosofija. Tai yra valdymo mechanizmai, pagrįsti nuolatinio kokybės gerinimo idėja ir jos veikimu bei laipsnišku įgyvendinimu. Kaizeno strategija remiasi teiginiu, kad gamybos procesų tobulinimui nėra ribų ir kiekviena įmonė, nepaisydama savo konkurencingumo, turi judėti į priekį.
- „Six Sigma“koncepcija pagrįsta tuo, kad gamybą galite valdyti naudodamiesi bet kokių duomenų pamatavimo principu. Kadangi gamybos procesai yra matuojami, juos galima stebėti ir patobulinti, analizuojant, pavyzdžiui, pagrindinius veiklos rodiklius KPI. Koncepcija skirta padaryti visus gamybos procesus nuspėjamais ir nuspėjamais, pagerinti esamus ir sukurti naujus optimizavimo algoritmus.
- Pagerinti gamybos efektyvumą, pagerinti pagaminto produkto kokybę ir sumažinti išlaidas - tai yra „Lean Manufacturing“sistemos uždaviniai.
Kartu šios trys sąvokos parodo, kaip palaipsniui ir nuolat gerinti gamybos procesų ir galutinio produkto kokybę, nepatiriant nereikalingų išlaidų.
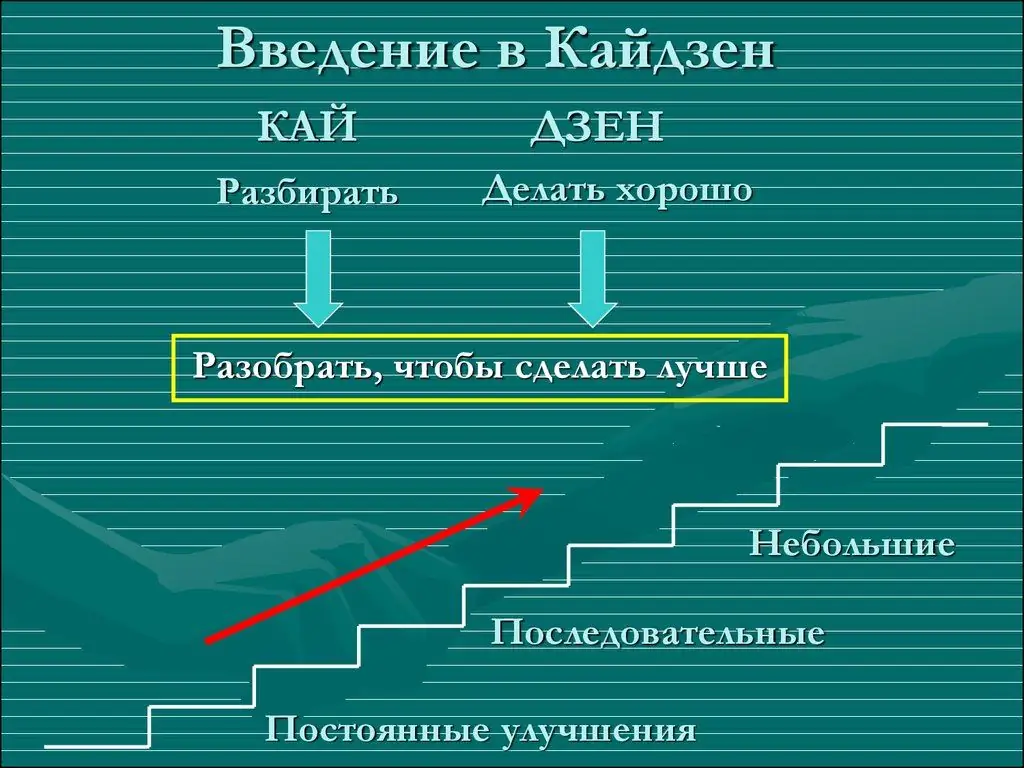
Taigi radikalumą gamybos valdyme pakeitė integruota filosofija, kurioje naudojami idealistiniai įmonės valdymo metodų principai ir įgyvendinamos efektyvios darbo tobulinimo metodikos ir įrankiai.
Liesos priemonės
Lean technologijos yra naudojamos visuose įmonės veiklos etapuose - nuo pirminio gamybos procesų projektavimo iki produktų pardavimo vartotojui.
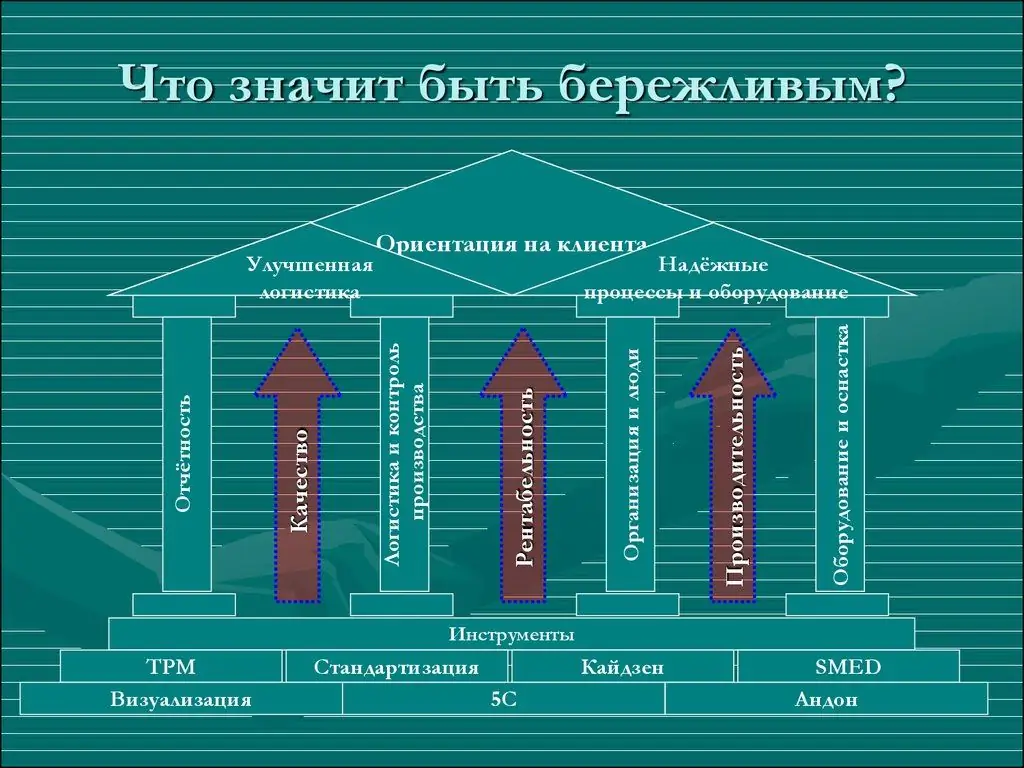
Nuolatinis optimizavimo procesas atliekamas naudojant „Lean“įrankius:
- Bendra produktyvi įrangos priežiūra - TPM (Total Productive Maintenance).
- Greitas perjungimas ir įrangos perkvalifikavimas „per vieną minutę“ir „vienu paspaudimu“- SMED („Single Minute Die of Die“) ir OTED („One Touch Change of Dies“).
- Nuolatinio medžiagų srauto organizavimas - CANBAN.
- Traukite gamybą - traukite gamybą.
- Vertės srauto atvaizdavimas - VSM („Value Stream Mapping“).
- Medžiagų valdymo sistema „pačiu laiku“- JIT (Just-In-Time).
- Vaizdinio valdymo ir grįžtamojo ryšio sistema Andon.
- Darbų vykdymo standartizavimas - SOP standartiniai darbo procesai.
- Efektyvios darbo vietos sukūrimo technologija - 5S arba 5S -CANDO.
- Visuotinės kokybės valdymo sistema - TQM (Total Quality Management).
Liesos priemonės veikia taip, kad darbo kokybės pagerėjimas būtų maksimaliai padidintas ir įvertintas visais gamybos etapais ir lygiais.